Ford Ecosport: Automatic Transmission - 6-Speed Automatic Transmission – 6F35 / Overhaul - Transmission
Special Tool(s) /
General Equipment
 |
100-001
(T50T-100-A)
Slide Hammer |
 |
100-002
(TOOL-4201-C)
Holding Fixture with Dial Indicator Gauge |
 |
205-153
(T80T-4000-W)
Handle |
 |
205-990 Installer, Axle Seal TKIT-2012A-FL TKIT-2012A-ROW |
 |
211-061
(T78P-3504-N1)
Remover, Roll Pin |
 |
303-D011
(D80L-100-G)
Actuator Pin (Dia 3/16) |
 |
303-D019
(D80L-100-Q)
Collet, 3/4 to 7/8 |
 |
307-003
(T57L-500-B)
Holding Fixture, Transmission |
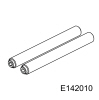 |
307-091 Handle, Torque Converter TKIT-2009TC-F |
 |
307-300 Gauge Bar, Shim Selection TKIT-1994-LMH/MH2 TKIT-1994-F TKIT-1994-FLM/FM |
 |
307-566 Retainer, Torque Converter TKIT-2006C-FFMFLM TKIT-2006C-LM TKIT-2006C-ROW |
 |
307-574 Forward Clutch Spring Compressor TKIT-2006UF-FLM TKIT-2006UF-ROW |
 |
307-578 Input Shaft Support Seal Installer (Back Plate, Multiple rings) TKIT-2006UF-FLM TKIT-2006UF-ROW |
 |
307-581 Manual lever seal installer TKIT-2006UF-FLM TKIT-2006UF-ROW |
 |
307-584 2-6 Spring Compressor TKIT-2006UF-FLM TKIT-2006UF-ROW |
 |
307-589 Overdrive clutch and balance piston service set TKIT-2006UF-FLM TKIT-2006UF-ROW |
 |
307-627 Installer, Converter Seal TKIT-2008ET-FLM TKIT-2008ET-ROW |
 |
307-628 Protector, Low Reverse Piston Seal TKIT-2008ET-FLM TKIT-2008ET-ROW |
 |
307-629 Protector, Low Reverse / 1-2-3-4 Piston Seal TKIT-2008ET-FLM TKIT-2008ET-ROW |
 |
307-630 Center Support Piston Spring Tool TKIT-2008ET-FLM TKIT-2008ET-ROW |
 |
307-632 Protector, 2-6 Piston Seal TKIT-2008ET-FLM TKIT-2008ET-ROW |
 |
307-633 2-6 Piston return spring Comp TKIT-2008ET-FLM TKIT-2008ET-ROW |
 |
307-635 Protector, Turbine Shaft Seal TKIT-2008ET-FLM TKIT-2008ET-ROW |
 |
307-691 Tester, Torque Convertor Leak |
 |
307-718 Installer, Axle Seal TKIT-2013B-FL TKIT-2013B-ROW |
 |
307-718-01 Adaper, 307-718 |
 |
307-723 Installer, Turbine Seal TKIT-2014A-FL |
 |
307-724 Seal Protector, Center Support |
 |
307-725 Mounting Fixture, Bench |
 |
307-732 Tool Kit, Torque Converter Flusher |
Flat Headed Screw Driver |
Hydraulic Press |
Hot Air Gun |
Long Nose Pliers |
Puller |
Punch |
Materials
Name |
Specification |
Motorcraft® Ultra Silicone Sealant TA-29 |
WSS-M4G323-A8
|
Motorcraft® MERCON® LV Automatic Transmission Fluid XT-10-QLVC |
WSS-M2C938-A MERCON® LV,
|
All vehicles
-
For information on component views and base part numbers.
Refer to: Transmission Description (307-01B Automatic Transmission -
6-Speed Automatic Transmission – 6F35, Description and Operation).
-
Install the special tool.
Use Special Service Tool: 307-725
Mounting Fixture, Bench.
-
Mount the transmission to the bench-mounted holding fixture.
Use Special Service Tool: 307-003
(T57L-500-B)
Holding Fixture, Transmission.
, 307-725
Mounting Fixture, Bench.
-
Remove the special tool.
Use Special Service Tool: 307-566
Retainer, Torque Converter.
-
NOTICE:
The torque converter is heavy. Be careful not to drop it or damage will result.
Using the special tools, remove the torque converter from the transmission.
Use Special Service Tool: 307-091
Handle, Torque Converter.
-
A new or remanufactured torque converter must be installed if one or more of the following statements are true:
-
The sealing surface has a groove worn from the seal.
-
A torque converter malfunction has been determined based on complete diagnostic procedures.
-
The torque converter stud or studs, threaded pads, impeller hub or bushing are damaged.
-
The torque converter exhibits external discoloration (due to overheating).
-
There is evidence of water or antifreeze contamination.
Flush The Torque Converter With The Transmission Cooling System Heated Flusher
-
NOTE:
Use transmission fluid specified for this
transmission. Do not use any supplemental transmission fluid additives
or cleaning agents. The use of these products could cause internal
transmission components to fail, which will affect the operation of the
transmission.
The torque converter must be flushed every time the
transmission is overhauled. It is mandatory that proper equipment and
procedures be followed when flushing the torque converter. The flushing
equipment used MUST:
-
Maintain the transmission fluid at 140°F or above
-
Pulsate the transmission fluid during cleaning
-
Have a filter with a rating of 100 micron or less
-
Have air purge capability before and after flushing
-
If equipment meeting the specifications above is not
available, the torque converter must be flushed by hand. Go to Flush The
Torque Converter By Hand steps later in this procedure.
-
Check and top off the transmission fluid level of the
transmission cooling system heated flusher with transmission fluid.
-
Turn on the heater and allow the transmission fluid in
the transmission cooling system heated flusher 15-30 minutes to heat up
to 60°C (140°F) before using.
-
Place the torque converter in an arbor press. Support the torque converter on the mounting pads.
-
Using the special tools, assemble the correct turbine
shaft simulator to the torque converter flush main hub and place it on
the torque converter hub.
Use Special Service Tool: 307-732
Tool Kit, Torque Converter Flusher.
-
Using the special tool, install the slotted cap.
Use Special Service Tool: 307-691
Tester, Torque Convertor Leak.
-
Apply enough force from the press to seal the torque converter flush main hub to the torque converter hub.
-
Connect the flush machine to the main hub.
-
Red hose on top.
-
Blue hose on bottom.
-
Follow the equipment instructions to purge transmission
fluid from the torque converter prior to starting the flushing
procedure.
-
WARNING:
The torque converter, adaptor 307-732, and the hoses will be hot.
NOTE:
Maintain visual contact with torque converter during
the entire flush procedure. Immediately stop the flush machine if a
leak develops. Repeat set up steps to reseal the tool to the converter
hub and continue flushing.
Forward flush the converter for 15 minutes.
-
Monitor GPM flow meter periodically during the flush
procedure. Flow rate above 2.0 gallons per minute is required to break
up and dislodge any contamination trapped behind the TCC plate. Service flush machine filter(s) if flow rate drops below 2 GPM.
-
Follow the equipment instructions to purge the torque converter.
-
WARNING:
The torque converter, adaptor 307-732, and the hoses will be hot.
Allow torque converter and equipment to cool for 30 minutes before handling.
-
Disconnect the hoses and remove the special tools.
Flush The Torque Converter By Hand
NOTICE:
Do not use water-based cleaners or mineral spirits to clean
or flush the torque converter or transmission damage will occur. Use
only clean transmission fluid designated for the transmission and torque
converter being serviced.
NOTE:
Only flush the torque converter by hand when the transmission cooling system heated flusher is not available.
-
Pour a small amount of transmission fluid from the
torque converter onto an absorbent white tissue or through a paper
filter.
-
Examine the transmission fluid for contaminants. The
transmission fluid must be free of metallic contaminants. If metallic
contaminants are present, do not continue with hand flushing. The torque
converter must be flushed with the transmission cooling system heated
flusher.
-
Drain the remaining transmission fluid from the torque converter.
-
Using only the recommended transmission fluid, add 1.9L
(2 qt) of clean transmission fluid into the converter and agitate by
hand.
Material: Motorcraft® MERCON® LV Automatic Transmission Fluid
/ XT-10-QLVC
(WSS-M2C938-A)
(MERCON® LV, )
-
Thoroughly drain the transmission fluid.
Auto-Start-Stop
-
NOTICE:
Do not use power tools to remove the transmission fluid auxiliary pump bolts or damage can occur.
NOTE:
Be prepared to collect escaping fluid.
Remove the bolts and the transmission fluid auxiliary pump.
-
Apply heat to the bolts to soften the Loctite®.
Use the General Equipment: Hot Air Gun
-
Remove and discard the bolts.
-
Remove the transmission fluid auxiliary pump gasket.
-
Remove the transmission fluid auxiliary pump supply tube assembly.
All vehicles
-
NOTE:
Note the location of the stud bolts for assembly.
Remove the main control cover bolts and the main control cover.
-
Disconnect the OSS sensor electrical connector.
-
Disconnect the TR sensor electrical connector.
-
Remove the main control-to-cover seal.
-
NOTE:
Note the location of the short and long main control-to-transmission case bolts for reassembly.
Remove the main control nut and the main
control-to-transmission case bolts and remove the main control assembly.
-
Inspect the main control assembly for damage. If damage
is found install a new main control assembly. If the main control
assembly is not damaged, disassemble the main control assembly and clean
it.
Refer to: Main Control Valve Body (307-01B Automatic Transmission - 6-Speed Automatic Transmission – 6F35, Overhaul).
-
Remove and discard the main control-to-transmission case separator plate (7J236).
-
Remove and discard the forward (1, 2, 3, 4) clutch and
low/reverse clutch main control-to-transmission case seals (7J135).
-
Remove the TSS sensor bolt and the TSS sensor.
-
Remove the TR sensor detent spring bolt and the TR sensor detent spring.
-
Remove the OSS sensor bolt and the OSS sensor.
-
NOTE:
Note the location of the stud bolts for assembly.
Remove the torque converter housing bolts.
-
Pry the torque converter housing loose from the transmission case.
-
Remove the torque converter housing from the transmission case.
-
Remove the No. 15 differential thrust bearing.
-
Remove the differential assembly.
-
Check that the bearings spin freely and do not move back
and forth or side to side excessively. Check for damage or excessive
wear. Install a new differential, if necessary.
-
Remove the differential sun gear.
-
Inspect the differential sun gear for damage or wear and install new, as necessary.
-
NOTE:
If the transmission plastic baffle has melted due to
overheat condition the transmission and the cooler must be replaced,
the plastic cannot be cleaned out of a cooler even with the heated
cooler flusher.
Remove the differential transmission fluid baffle.
-
-
Remove the No. 13 thrust washer.
-
Remove the No. 11 drive sprocket thrust bearing.
-
Simultaneously remove the drive and driven sprockets and the chain.
-
Remove the drive chain from the drive and driven sprockets.
-
Clean and inspect the drive chain for damage or excessive wear and install new, if necessary.
-
Check for stretching or tightness of the chain links.
-
Check that the chain moves freely.
-
Inspect the driven sprocket for damage or excessive wear and install new, if necessary.
-
Remove the snap ring and remove the drive sprocket from the front planetary hub/park gear assembly.
-
Inspect the drive sprocket for damage or excessive wear and install new, if necessary.
-
Inspect the front planetary hub/park gear assembly for damage or excessive wear and install new, if necessary.
-
Install the drive sprocket on the front planetary hub/park gear assembly and install the snap ring.
-
Install the drive chain on the drive and driven sprockets.
-
-
Remove the No. 12 driven sprocket thrust bearing.
-
Remove the No. 10 front sun gear and shell assembly thrust bearing.
-
Remove the transmission fluid baffle bolts and the transmission fluid baffle.
-
Remove the park pawl pin and spring.
-
Remove the park pawl.
-
NOTE:
The forward (1, 2, 3, 4) clutch snap ring is
beveled. The beveled side of the snap ring goes up (flat side down).
NOTE:
The forward (1, 2, 3, 4) clutch snap ring gap faces the front of the transmission.
Remove the forward (1, 2, 3, 4) clutch snap ring.
-
Remove the forward (1, 2, 3, 4) clutch pressure plate, clutch assembly and wave springs.
-
Inspect the clutch plate and pressure plate surfaces for damage or excessive wear.
-
Remove the front planetary sun gear and shell assembly.
-
Clean and inspect the front planetary sun gear and shell
assembly for damage or wear and install new, as necessary.
-
Shell-to-clutch pack surfaces
-
Remove the front planetary carrier/rear ring gear assembly.
-
Clean and inspect the front planetary carrier/rear ring
gear assembly for damage or excessive wear and install new, as
necessary.
-
-
Remove the No. 7 thrust bearing.
-
Remove the No. 8 thrust bearing.
-
Remove the center planetary carrier/front ring gear assembly.
-
Clean and inspect the center planetary carrier/front
ring gear assembly for damage or excessive wear and install new, as
necessary.
-
Remove the center planetary sun gear.
-
Clean and inspect the center planetary sun gear for damage or excessive wear and install new, as necessary.
-
-
Remove the No. 5 thrust bearing.
-
Remove the No. 6 thrust bearing.
-
Remove the center support assembly.
-
Remove the rear planetary carrier/center ring gear assembly.
-
Clean and inspect the rear planetary carrier/center ring
gear assembly for damage or excessive wear and install new, as
necessary.
-
Remove the low/reverse wave spring, clutch pack and pressure plate.
-
Inspect the low/reverse clutch pack and pressure plate
surface for damage or excessive wear and install new, if necessary.
-
Remove the low One-Way Clutch (OWC).
-
NOTICE:
Do not clean in water or with water-based solvents. Damage to the component may occur.
NOTE:
The low One-Way Clutch (OWC) should not be disassembled.
Clean and inspect the low One-Way Clutch (OWC) for
cracks and damaged splines. The internal splined section should rotate
clockwise and lock when rotated counterclockwise. If any damage is found
or the clutch does not rotate or lock, install a new low One-Way Clutch
(OWC).
-
Inspect the intermediate (2, 6) clutch surface for
damage. If the surface is burned or worn excessively, install a new low
One-Way Clutch (OWC).
-
NOTE:
The intermediate (2, 6) clutch is removed with the rear planetary sun gear and shell assembly.
Remove the rear planetary sun gear and shell assembly
and remove the intermediate (2, 6) clutch from the assembly.
-
Inspect the intermediate (2, 6) clutch surface for damage or excessive wear and install new, if necessary.
-
Clean and inspect the rear planetary sun gear and shell
assembly for damage or wear and install new, if necessary.
-
Shell-to-clutch pack surfaces
-
Remove the steel plate and the wave spring
-
Inspect the pressure plate surface for damage or excessive wear and install new, if necessary.
-
Remove the No. 3 thrust bearing.
-
Remove the overdrive/direct clutch assembly.
-
NOTE:
If the No. 1 thrust bearing is stuck to the
overdrive/direct clutch assembly, remove the No. 1 thrust bearing from
the overdrive/direct clutch assembly.
Remove the No. 1 thrust bearing.
-
Remove the intermediate (2, 6) clutch apply ring.
-
Remove the clutch support tower bolts and the clutch support tower.
-
NOTE:
Note the location of the snap ring gap for assembly.
Remove the intermediate (2, 6) clutch return spring snap ring.
-
NOTE:
Note the position of the return spring for assembly.
Remove the intermediate (2, 6) clutch return spring.
-
Remove and discard the intermediate (2, 6) clutch piston (7F472).
Use the General Equipment: Long Nose Pliers
-
Remove and discard the clutch feed seals (7N265).
-
Remove the manual control lever nut and the manual control lever from the manual control shaft.
-
NOTICE:
Do not drive the manual control shaft pin through
the manual control shaft. The manual control shaft pin will contact the
transmission case causing damage to the transmission case.
Using the special tool, pull the manual control shaft pin (7G100) out of the manual control shaft.
Use Special Service Tool: 211-061
(T78P-3504-N1)
Remover, Roll Pin.
-
Remove the manual control shaft.
-
Remove the TR sensor and the park pawl actuator rod and remove the park pawl actuator rod from the TR sensor.
-
Remove and discard the manual control shaft seal (7F337).
Use the General Equipment: Flat Headed Screw Driver
-
Remove and discard the LH halfshaft seal (7H260).
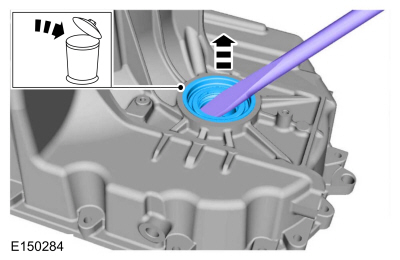 |
|
-
-
NOTICE:
If the LH transmission case bushing or the LH halfshaft bushing surface
shows signs of excessive wear or damage, a new LH transmission case
bushing and a new LH halfshaft must be installed, or transmission
failure can occur.
Clean and inspect the LH transmission case bushing and the bushing
surface on the LH halfshaft for damage or excessive wear. If the LH
transmission case bushing or the LH halfshaft shows signs of excessive
wear or damage, install new components.
Refer to: Transmission Case (307-01B Automatic Transmission - 6-Speed
Automatic Transmission – 6F35, Disassembly and Assembly of
Subassemblies).
-
NOTICE:
Do not use metal scrapers, wire brushes, power
abrasive discs, or other abrasive means to clean sealing surfaces. These
tools cause scratches and gouges which make leak paths.
Make sure that the mating faces are clean and free of foreign material.
Refer to: RTV Sealing Surface Cleaning and Preparation (303-00 Engine System - General Information, General Procedures).
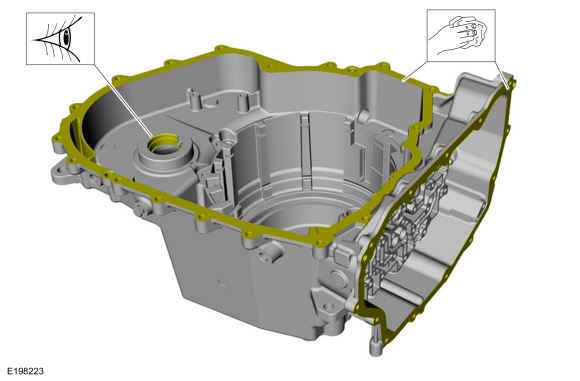 |
|
-
Remove the pump-to-torque converter housing bolts and the pump and filter assembly.
-
Remove and discard the RH halfshaft seal (1177).
-
-
Inspect the torque converter housing and the
differential ring gear for damage or excessive wear. If the differential
ring gear shows signs of excessive wear or damage replace the
differential ring gear.
Refer to: Transmission Case (307-01B Automatic Transmission - 6-Speed
Automatic Transmission – 6F35, Disassembly and Assembly of
Subassemblies).
-
NOTICE:
Do not use metal scrapers, wire brushes, power
abrasive discs, or other abrasive means to clean sealing surfaces. These
tools cause scratches and gouges which make leak paths.
Make sure that the mating faces are clean and free of foreign material.
Refer to: RTV Sealing Surface Cleaning and Preparation (303-00 Engine System - General Information, General Procedures).
-
NOTE:
Note the orientation of the transmission fluid filter to the fluid pump assembly.
Rotate the transmission fluid filter 90 degrees
clockwise and pull the transmission fluid filter out of the pump
assembly and discard the filter (7G186).
-
Assemble the special tools and remove and discard the input shaft seal (7048).
Use Special Service Tool: 100-001
(T50T-100-A)
Slide Hammer.
, 303-D011
(D80L-100-G)
Actuator Pin (Dia 3/16).
, 303-D019
(D80L-100-Q)
Collet, 3/4 to 7/8.
-
Remove the pump assembly-to-torque converter housing O-ring seal (7D441, ID 152mm).
-
Remove the torque converter hub seal snap ring.
-
Using a dent puller, remove the torque converter hub seal (7A248).
Use the General Equipment: Puller
-
Position the pump assembly in the torque converter
housing and install 2 pump-to-torque converter housing bolts hand-tight.
-
Loosen the pump bolts.
-
Remove the pump-to-torque converter housing bolts and the pump assembly from the torque converter housing.
-
Remove the pump bolts and separate the pump assembly halves.
-
NOTE:
The dot on the inner pump gear faces up.
Remove the pump gears.
-
Compress the main pressure regulator valve spring with a screwdriver and remove the retainer with a magnet.
Use the General Equipment: Flat Headed Screw Driver
-
Install a M4 bolt in the valve and remove the main pressure regulator valve assembly.
-
Compress the TCC control valve spring with a screw driver and remove the retainer with a magnet.
Use the General Equipment: Flat Headed Screw Driver
-
Remove the TCC control valve assembly.
-
Clean and dry all of the pump assembly components.
-
Inspect the inner and the outer pump gears for damage or excessive wear and install new, if necessary.
-
Inspect the pump housing for damage or excessive wear and install new, as necessary.
-
Inner and outer pump gear to pump housing surface.
-
Inspect the torque converter hub bushing for damage or excessive wear and install new, as necessary.
-
-
Inspect the aluminum pump housing near the TCC control valve for scoring or blockage.
-
Using a straight edge, inspect the aluminum pump housing near the TCC
control valve for evidence of any surface warping possibly causing
internal pressure leaks. Inspect the hydraulic passages for blockage.
-
NOTE:
Make sure the valves and the pump housing are clean and dry.
Install the TCC
control valve and the main pressure regulator valve in the pump
housing. Verify each valve moves freely in the pump housing bore and
falls out under its own weight.
-
Using a straight edge, inspect the pump housing for evidence of surface warping at the case to pump seal area.
-
Inspect the stator bushing for damage or excessive wear and install new, as necessary.
-
Inspect the turbine shaft support bushing for wear or
scoring that might cause pressure leaks and install new, as necessary.
-
NOTE:
The TCC control valve retainer is shown assembled in the pump body, the main pressure regulator valve retainer is similar.
Assemble the TCC
control valve assembly and main pressure regulator valve assembly and
install the valves in the pump. Compress the valve springs with a screw
driver and install the retainers.
-
NOTE:
The dot on the inner pump gear faces up.
Install the pump gears.
-
Position the stator support on the pump housing and install the pump bolts hand-tight.
-
Install the pump assembly in the torque converter
housing and install 2 pump-to-torque converter housing bolts hand-tight.
-
Tighten the pump bolts.
Torque:
89 lb.in (10 Nm)
-
Remove the pump-to-torque converter housing bolts and the pump assembly from the torque converter housing.
-
Install a new torque converter hub seal on the special tool.
Use Special Service Tool: 307-627
Installer, Converter Seal.
-
Using the special tool, install a new torque converter hub seal.
Use Special Service Tool: 307-627
Installer, Converter Seal.
-
Install the torque converter hub seal snap ring.
-
Install a new pump assembly-to-torque converter housing O-ring seal.
-
Install a new input shaft seal on the special tool.
Use Special Service Tool: 307-723
Installer, Turbine Seal.
-
Using the special tool, install the input shaft seal.
Use Special Service Tool: 307-723
Installer, Turbine Seal.
-
Lubricate the transmission fluid filter o-ring with transmission fluid.
Material: Motorcraft® MERCON® LV Automatic Transmission Fluid
/ XT-10-QLVC
(WSS-M2C938-A)
(MERCON® LV, )
-
Clean the magnet on the transmission fluid filter.
-
Install a new transmission fluid filter.
-
Position the transmission fluid filter in the pump assembly.
-
Rotate the transmission fluid filter counterclockwise 90 degrees.
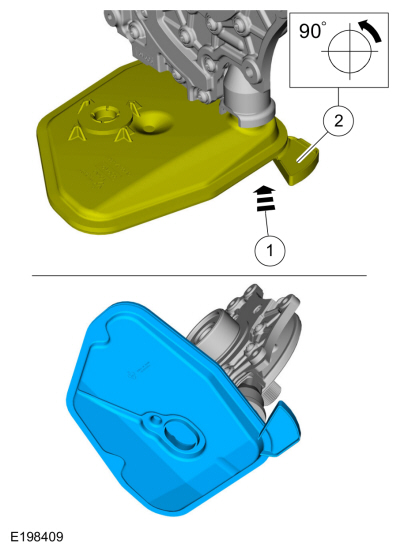 |
|
-
NOTICE:
The piston return spring, snap ring or snap ring
retainer from the low/reverse clutch side of the center support are not
interchangeable with the forward clutch side of the center support. When
disassembling the center support, be careful not to mix the components
from the low/reverse clutch side with the forward clutch side of the
center support. Failure to assemble the center support with the
components in the correct side will result in damage to the center
support, low/reverse or forward clutch.
NOTE:
The low/reverse clutch piston in the center support is the side of the center support with the long legs.
Using the special tool and a press, compress the
low/reverse clutch return spring and remove the snap ring and the snap
ring retainer.
Use Special Service Tool: 307-630
Center Support Piston Spring Tool.
Use the General Equipment: Hydraulic Press
-
Remove the low/reverse clutch return spring.
-
Apply 172 kPa (25 psi) of air pressure to the
low/reverse clutch piston port and remove and discard the low/reverse
clutch piston (7D402).
-
NOTE:
The forward clutch piston in the center support is the side of the center support with the short legs.
Using the special tool and a press, compress the forward
(1,2, 3, 4) clutch return spring and remove the snap ring and the snap
ring retainer.
Use Special Service Tool: 307-630
Center Support Piston Spring Tool.
Use the General Equipment: Hydraulic Press
-
Remove the return spring from the forward (1, 2, 3, 4) clutch piston.
-
Apply 172 kPa (25 psi) of air pressure to the forward
(1, 2, 3, 4) clutch piston port and remove and discard the forward (1,
2, 3, 4) clutch piston (7A262).
-
Clean and inspect the center support for damage. Install a new center support if necessary.
-
NOTE:
The forward clutch piston in the center support is the side of the center support with the short legs.
Install the special tools on the forward clutch piston side of the center support.
Use Special Service Tool: 307-724
Seal Protector, Center Support.
, 307-629
Protector, Low Reverse / 1-2-3-4 Piston Seal.
-
Material: Petroleum Jelly
Lubricate the sealing surfaces of a new forward (1, 2, 3, 4) clutch piston with petroleum jelly.
-
Position the forward (1, 2, 3, 4) clutch piston on the special tools and push it down into the center support.
Use Special Service Tool: 307-724
Seal Protector, Center Support.
, 307-629
Protector, Low Reverse / 1-2-3-4 Piston Seal.
-
NOTICE:
The piston return spring, snap ring or snap ring
retainer from the low/reverse clutch side of the center support are not
interchangeable with the forward clutch side of the center support. When
assembling the center support, be careful not to mix the components
from the low/reverse clutch side with the forward clutch side of the
center support. Failure to assemble the center support with the
components in the correct side will result in damage to the center
support, low/reverse or forward clutch.
NOTE:
The forward clutch piston return spring has a
slightly larger outer diameter and narrower teeth compared to the
Low/Reverse piston return spring.
Install the forward (1, 2, 3, 4) clutch piston return spring.
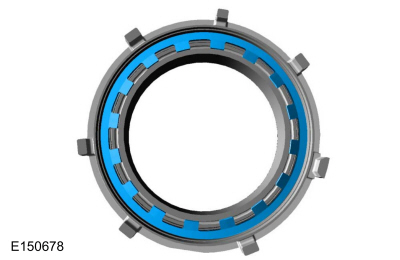 |
|
-
NOTE:
The forward clutch snap ring retainer has a slightly
larger outer diameter and is slightly wider compared to the Low/Reverse
clutch snap ring retainer.
NOTE:
The forward clutch snap ring has square cut ends
compared to the Low/Reverse clutch snap ring's notched ends.
Using the special tools and a press, compress the
forward (1,2, 3, 4) clutch return spring and install the snap ring
retainer and the snap ring.
Use Special Service Tool: 307-630
Center Support Piston Spring Tool.
Use the General Equipment: Hydraulic Press
-
Inspect the snap ring to be sure it is seated in the groove on the center support.
Use the General Equipment: Flat Headed Screw Driver
-
NOTE:
Use 307-628/1 on the inside diameter and use 307-724 on the outside diameter.
Turn the center support over and install the special
tools on the low/reverse piston side of the center support.
Use Special Service Tool: 307-724
Seal Protector, Center Support.
, 307-628
Protector, Low Reverse Piston Seal.
-
Material: Petroleum Jelly
Lubricate the sealing surfaces of a new low/reverse piston with petroleum jelly.
-
NOTE:
Use 307-628/1 on the inside diameter and use 307-724 on the outside diameter.
Position the low/reverse clutch piston on the special tools and push it down into the center support.
Use Special Service Tool: 307-724
Seal Protector, Center Support.
, 307-628
Protector, Low Reverse Piston Seal.
-
Install the low/reverse piston return spring.
-
Using the special tools and a press, compress the
low/reverse clutch return spring and install the snap ring retainer and
the snap ring.
Use Special Service Tool: 307-630
Center Support Piston Spring Tool.
Use the General Equipment: Hydraulic Press
-
Inspect the snap ring to be sure it is seated in the groove on the center support.
Use the General Equipment: Flat Headed Screw Driver
-
Remove and discard the 4 Teflon® seals (7C565).
-
Clean and inspect the clutch support tower for damage. Install a new clutch support tower if damaged.
-
Install the special tool on the clutch support tower and
adjust the special tool to align the bottom edge of the tool with the
top edge of the bottom Teflon® seal groove.
Use Special Service Tool: 307-578
Input Shaft Support Seal Installer (Back Plate, Multiple rings).
-
Install a new Teflon® seal on the special tool.
Use Special Service Tool: 307-578
Input Shaft Support Seal Installer (Back Plate, Multiple rings).
-
Install the special tool 307-578/2 over 307-578/3. Using
the special 307-578/2, slide the Teflon® seal over the clutch support
tower and into the groove.
Use Special Service Tool: 307-578
Input Shaft Support Seal Installer (Back Plate, Multiple rings).
-
Remove tools and repeat steps for the other 3 Teflon® seals.
Use Special Service Tool: 307-578
Input Shaft Support Seal Installer (Back Plate, Multiple rings).
-
Install the special tool on the clutch support tower to size the 4 Teflon® seals.
Use Special Service Tool: 307-578
Input Shaft Support Seal Installer (Back Plate, Multiple rings).
-
Remove the input shaft snap ring.
-
Remove the input shaft.
-
Remove the overdrive (4, 5, 6) clutch hub.
-
Remove the overdrive (4, 5, 6) clutch hub, No. 2 thrust bearing.
-
Remove the overdrive (4, 5, 6) clutch snap ring.
-
Remove the overdrive (4, 5, 6) clutch pressure plate and clutch assembly.
-
Inspect the clutch plate and pressure plate surfaces for damage or excessive wear.
-
Install the special tools on the balance piston.
Use Special Service Tool: 307-584
2-6 Spring Compressor.
, 307-589
Overdrive clutch and balance piston service set.
-
Using a press, compress the overdrive (4, 5, 6) clutch return spring and remove the snap ring.
Use Special Service Tool: 307-584
2-6 Spring Compressor.
, 307-589
Overdrive clutch and balance piston service set.
Use the General Equipment: Hydraulic Press
-
Remove and discard the balance piston (7J029).
-
Remove the overdrive (4, 5, 6) piston return spring.
-
Install the clutch support tower in the transmission case and install the clutch support tower bolts.
Torque:
124 lb.in (14 Nm)
-
Remove the special tool.
Remove Special Service Tool: 307-578
Input Shaft Support Seal Installer (Back Plate, Multiple rings).
-
Install the No. 1 overdrive/direct clutch assembly thrust bearing.
-
Position the overdrive/direct clutch assembly in the transmission case.
-
Apply compressed air to the overdrive (4, 5, 6) clutch
piston port and remove the overdrive (4, 5, 6) clutch piston.
-
Remove the overdrive/direct clutch assembly from the transmission case.
-
Remove and discard the overdrive (4, 5, 6) clutch piston seal from the overdrive/direct clutch assembly.
-
Remove and discard the seals (7A548, 7J008) from the overdrive (4, 5, 6) clutch piston.
-
NOTICE:
Only compress the direct clutch piston return spring
far enough to take the tension from the direct clutch cylinder off the
snap ring. If the piston is compressed too far, the piston alignment tab
may be broken off.
Install the special tools on the direct (3, 5, R) clutch
cylinder. Using a press, compress the direct (3, 5, R) clutch piston
return spring, and remove the snap ring.
-
Do not contact the overdrive/direct clutch hub and
shaft assembly with the direct (3, 5, R) clutch cylinder.
-
Remove the snap ring.
Use Special Service Tool: 307-584
2-6 Spring Compressor.
, 307-589
Overdrive clutch and balance piston service set.
Use the General Equipment: Hydraulic Press
-
Remove the direct (3, 5, R) clutch cylinder.
-
Remove and discard the direct (3, 5, R) clutch piston (7F254).
-
NOTE:
Note the position of the return spring for assembly. The flat side faces down.
Remove the direct (3, 5, R) clutch piston return spring.
-
Remove the direct (3, 5, R) clutch snap ring.
-
Slightly lift up on the direct (3, 5, R) clutch so that the snap ring floats freely.
-
Using a tool, compress the snap ring.
-
Allow the direct (3, 5, R) clutch and pressure plate
to drop so that the snap ring is out of the pressure plate groove.
-
Remove the snap ring.
-
Remove the direct (3, 5, R) clutch pressure plate, clutch pack and wave spring.
-
Inspect the clutch plate and pressure plate surfaces for damage or excessive wear.
-
Remove and discard the direct (3, 5, R) clutch piston seals (7E056, 7F234, 7C000).
-
Clean and inspect the overdrive/direct clutch assembly
for damage or excessive wear and install new components as necessary.
-
Material: Petroleum Jelly
Install new direct (3, 5, R) clutch piston seals and lubricate the seals with petroleum jelly.
-
Install the direct (3, 5, R) clutch wave spring.
-
Soak the direct (3, 5, R) clutch pack in transmission fluid.
Material: Motorcraft® MERCON® LV Automatic Transmission Fluid
/ XT-10-QLVC
(WSS-M2C938-A)
(MERCON® LV, )
-
Install the direct (3, 5, R) clutch assembly and pressure plate.
-
Install the direct (3, 5, R) clutch snap ring.
-
Compress the snap ring.
-
Lift the direct (3, 5, R) clutch so that the snap ring is in the groove of the pressure plate.
-
Release the tension on the snap ring.
-
NOTE:
Install the direct (3, 5, R) clutch piston return spring with the flat side facing down.
Install the direct (3, 5, R) clutch piston return spring.
-
Material: Petroleum Jelly
Lubricate a new direct (3, 5, R) clutch piston with petroleum jelly and install the piston.
-
Install the direct (3, 5, R) clutch cylinder.
-
NOTICE:
Only compress the direct clutch piston return spring
far enough to take the tension from the direct clutch cylinder off the
snap ring. If the piston is compressed too far, the piston alignment tab
may be broken off.
Install the special tools on the direct (3, 5, R) clutch
cylinder. Using a press, compress the direct (3, 5, R) clutch piston
return spring, and install the snap ring.
-
Do not contact the overdrive/direct clutch hub and
shaft assembly with the direct (3, 5, R) clutch cylinder.
-
Install the snap ring.
Use Special Service Tool: 307-584
2-6 Spring Compressor.
, 307-589
Overdrive clutch and balance piston service set.
Use the General Equipment: Hydraulic Press
-
Material: Petroleum Jelly
Install new seals on the overdrive (4, 5, 6) clutch piston and lubricate the seals with petroleum jelly.
-
Material: Petroleum Jelly
Install a new overdrive (4, 5, 6) clutch piston inner seal and lubricate the seal with petroleum jelly.
-
Position the overdrive (4, 5, 6) clutch piston in place.
-
Using the special tools, install the overdrive (4, 5, 6)
clutch piston into the overdrive/direct clutch assembly by hand.
Use Special Service Tool: 307-589
Overdrive clutch and balance piston service set.
-
NOTE:
Holes face up on the overdrive (4, 5, 6) clutch piston return spring.
Install the overdrive (4, 5, 6) clutch piston return spring.
-
Material: Petroleum Jelly
Lubricate the seals on a new balance piston with petroleum jelly and position the piston in place.
-
Install the special tools on the balance piston.
Use Special Service Tool: 307-584
2-6 Spring Compressor.
, 307-589
Overdrive clutch and balance piston service set.
-
Using a press, compress the overdrive (4, 5, 6) clutch return spring and install the snap ring.
Use Special Service Tool: 307-584
2-6 Spring Compressor.
, 307-589
Overdrive clutch and balance piston service set.
Use the General Equipment: Hydraulic Press
-
Install the No. 2 thrust bearing.
-
Install the overdrive (4, 5, 6) clutch hub.
-
Soak the overdrive (4, 5, 6) clutch pack in transmission fluid.
Material: Motorcraft® MERCON® LV Automatic Transmission Fluid
/ XT-10-QLVC
(WSS-M2C938-A)
(MERCON® LV, )
-
Install the overdrive (4, 5, 6) clutch pack.
-
Install the overdrive (4, 5, 6) clutch pressure plate.
-
Install the overdrive (4, 5, 6) clutch snap ring.
-
Install the input shaft.
-
While holding the input shaft in place, install the snap ring.
-
Position the overdrive/direct clutch assembly in the
transmission case, install the special tool or a dial indicator and
position the plunger on the overdrive (4, 5, 6) clutch pressure plate.
Use Special Service Tool: 100-002
(TOOL-4201-C)
Holding Fixture with Dial Indicator Gauge.
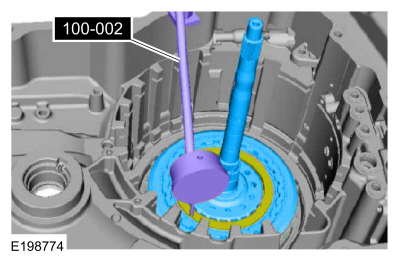 |
|
-
NOTE:
The dial indicator plunger is positioned on the overdrive (4, 5, 6) clutch pressure plate.
Apply 172 kPa (25 psi) of air pressure to the overdrive
(4, 5, 6) clutch piston port while recording the clutch pack clearance
on the Dial Indicator. The clearance should be between 0.95 mm (0.037
in) and 2.4 mm (0.09 in). If the clearance is out of range, check the
overdrive (4, 5, 6) clutch pack for correct installation. If the
overdrive (4, 5, 6) clutch pack is correctly installed, install a new
overdrive (4, 5, 6) clutch pack.
Refer to: Specifications (307-01B Automatic Transmission - 6-Speed Automatic Transmission – 6F35, Specifications).
Use Special Service Tool: 100-002
(TOOL-4201-C)
Holding Fixture with Dial Indicator Gauge.
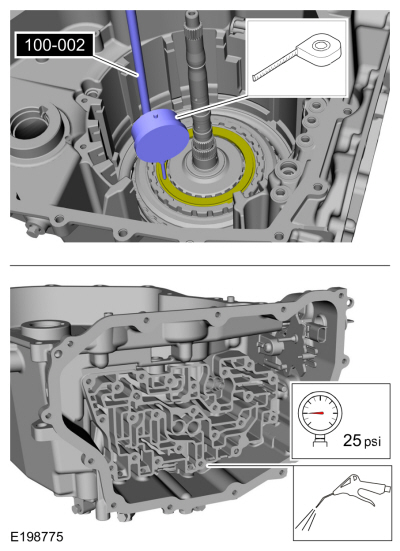 |
|
-
NOTE:
The direct clutch pressure plate travel is limited
by the snap ring and the top of the center support legs. Placing the
dial indicator on the pressure plate will not accurately measure total
clutch pack clearance.
Position the plunger on one of the top direct (3, 5, R)
clutch plate tabs. Apply 172 kPa (25 psi) of air pressure to the direct
(3, 5, R) clutch piston port while recording the clutch pack clearance
on Dial Indicator. The clearance should be between 2.46 mm (0.09 in) and
2.76 mm (0.10 in). If the clearance is out of range, check the direct
(3, 5, R) clutch pack for correct installation. If the direct (3, 5, R)
clutch pack is correctly installed, install a new direct (3, 5, R)
clutch pack.
Refer to: Specifications (307-01B Automatic Transmission - 6-Speed Automatic Transmission – 6F35, Specifications).
Use Special Service Tool: 100-002
(TOOL-4201-C)
Holding Fixture with Dial Indicator Gauge.
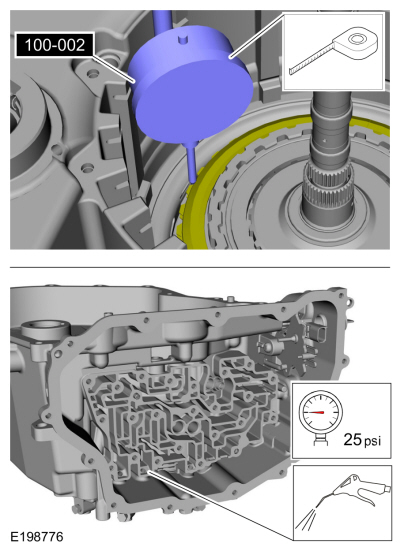 |
|
-
Remove the special tool, overdrive/direct clutch
assembly and the No. 1 overdrive/direct clutch assembly thrust bearing.
Remove Special Service Tool: 100-002
(TOOL-4201-C)
Holding Fixture with Dial Indicator Gauge.
-
Assemble the special tools. Install a new LH halfshaft seal on the special tool.
Use Special Service Tool: 205-153
(T80T-4000-W)
Handle.
, 205-990
Installer, Axle Seal.
-
Using the special tools, install the new LH halfshaft seal in the transmission case.
Use Special Service Tool: 205-153
(T80T-4000-W)
Handle.
, 205-990
Installer, Axle Seal.
-
Install a new manual control shaft seal on the special tool.
Use Special Service Tool: 307-581
Manual lever seal installer.
-
Using the special tool, install the new manual control shaft seal in the transmission case.
Use Special Service Tool: 307-581
Manual lever seal installer.
-
Install the special tool.
Use Special Service Tool: 307-632
Protector, 2-6 Piston Seal.
-
Lubricate the seals on the intermediate (2, 6) clutch piston with transmission fluid.
Material: Motorcraft® MERCON® LV Automatic Transmission Fluid
/ XT-10-QLVC
(WSS-M2C938-A)
(MERCON® LV, )
-
NOTICE:
Be sure the bleed hole is aligned in the correct
position as noted during disassembly or damage to the transmission can
occur.
Install the intermediate (2, 6) clutch piston on the
seal protector with the bleed hole aligned at the top of the
transmission case.
-
Position the intermediate (2, 6) clutch piston return
spring on the piston to align the piston before pushing it in its bore.
The tabs of the return spring should fit into the indentions of the
piston and the 2 outer tabs should be at the clockwise most position of
the open area at the bottom of the transmission case. The bleed hole on
the piston should be aligned between the inner double tabs of the return
spring.
-
Inner double tabs
-
Bleed hole
-
Outer tabs
-
Remove the intermediate (2, 6) clutch piston return spring.
-
Install the special tool on the intermediate (2, 6)
clutch piston. Push the intermediate (2, 6) clutch piston into the
clutch cylinder by hand.
Use Special Service Tool: 307-584
2-6 Spring Compressor.
-
NOTICE:
Be sure the return spring is positioned correctly
with the forward clutch bleed hole aligned between the inner double tabs
and the outer tab in the clockwise most position of the slot at the
bottom of the case or damage to the transmission can occur.
Install the intermediate (2, 6) clutch piston return
spring. The tabs of the return spring should fit into the indentions of
the piston and the 2 outer tabs should be at the clockwise most position
of the slot at the bottom of the case. The bleed hole on the piston
should be aligned between the inner double tabs of the return spring.
-
Inner double tabs
-
Bleed hole
-
Outer tabs
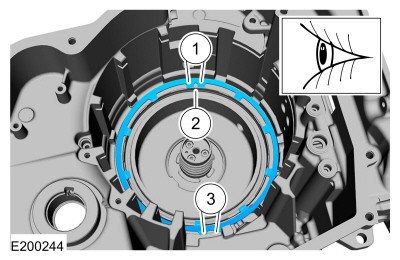 |
|
-
NOTICE:
Be sure the snap ring is aligned with the gap facing
the front of the transmission or damage to the transmission can occur.
The front of the transmission is where the low/reverse and forward (1,
2, 3,4) clutch hydraulic ports are located.
Position the snap ring in the transmission case just
above the snap ring groove. Align the gap of the snap ring to face the
front of the transmission.
-
Snap ring
-
Snap ring gap
-
Low/reverse and forward (1, 2, 3, 4) clutch hydraulic ports (located at the front of the transmission case)
-
Install the special tool on the transmission case to center the intermediate (2, 6) clutch return spring.
Use Special Service Tool: 307-633
2-6 Piston return spring Comp.
-
Install the special tool on the snap ring.
Use Special Service Tool: 307-633
2-6 Piston return spring Comp.
-
Install the special tool on the transmission case.
Use Special Service Tool: 307-574
Forward Clutch Spring Compressor.
-
NOTICE:
Be sure the return spring is centered or it can bind
on the snap ring groove and cause damage to the transmission case.
Using the special tools, install the intermediate (2, 6) clutch snap ring in the groove.
Use Special Service Tool: 307-574
Forward Clutch Spring Compressor.
, 307-633
2-6 Piston return spring Comp.
-
Install the intermediate (2, 6) clutch apply ring. Tap the ring in place.
-
NOTICE:
Be sure to install the No. 1 thrust bearing with the
flat side facing up or damage to the transmission can occur.
Install the No. 1 thrust bearing with rubber side facing
down and the tabs aligned with the notches in the case.
-
Install the overdrive/direct clutch assembly.
-
NOTICE:
Be sure to install the No. 3 thrust bearing with the
flat side facing down or damage to the transmission can occur.
Install the No. 3 thrust bearing with the flat side facing down.
-
Install the direct/intermediate clutch hub and rear sun gear assembly.
-
Install the intermediate (2, 6) wave spring assembly.
-
Soak the intermediate (2, 6) clutch assembly in transmission fluid.
Material: Motorcraft® MERCON® LV Automatic Transmission Fluid
/ XT-10-QLVC
(WSS-M2C938-A)
(MERCON® LV, )
-
Install the intermediate (2, 6) clutch assembly,
temporarily reversing the top friction and steel plates for the clutch
stack-up measurement.
-
Steel plate
-
Friction plate
-
Install the special tool on the transmission case.
Use Special Service Tool: 307-300
Gauge Bar, Shim Selection.
-
Using a 7-8" (375-400mm) depth gauge, measure and record
as measurement A, the distance from the special tool to the top of the
intermediate (2, 6) clutch pack at 3 different points and average the 3
distances.
Use Special Service Tool: 307-300
Gauge Bar, Shim Selection.
-
Using a depth gauge, measure and record as measurement
B, the distance from the top of the special tool to the transmission
case step above the intermediate (2, 6) clutch.
Use Special Service Tool: 307-300
Gauge Bar, Shim Selection.
-
Subtract measurement B from measurement A The clearance
should be between 0.220 mm (0.008in) and 1.84 mm (0.072 in). If the
clearance is out of range, check the intermediate (2, 6) clutch pack for
correct installation. If the intermediate (2, 6) clutch pack is
correctly installed, install a new clutch pack.
Description
|
Reading
|
Measurement A
|
|
Measurement B
|
|
Subtract measurement B from
measurement A and check to see if it is within range of 0.220 mm (0.008
in) and 1.84 mm (0.072 in)
|
|
-
NOTE:
When the intermediate (2, 6) clutch is correctly installed, a friction plate is on top.
Remove the top intermediate (2, 6) clutch friction and
steel plate and correctly install the plates back in the transmission
case.
-
Steel plate
-
Friction plate
-
NOTE:
Hold the low one way clutch square against the front
of the transmission during installation to prevent cocking/binding.
Install the One-Way Clutch (OWC) assembly.
-
Install the rear planetary carrier/center ring gear assembly.
-
NOTE:
Note the position of the low/reverse pressure plate.
When installing the center support, the long support legs must fit
through the low/reverse pressure plate and rest on the One-Way Clutch
(OWC).
NOTE:
The stepped side of the pressure plate is installed down facing the low one way clutch.
Position the low/reverse pressure plate so that the
center support legs fit through the pressure plate and rest on the
One-Way Clutch (OWC) and install the low/reverse pressure plate.
-
Soak the low/reverse clutch in transmission fluid.
Material: Motorcraft® MERCON® LV Automatic Transmission Fluid
/ XT-10-QLVC
(WSS-M2C938-A)
(MERCON® LV, )
-
Align the low/reverse clutch pack with the pressure
plate and install it in the transmission case temporarily reversing the
wave spring and top steel plate.
-
Steel plate.
-
Wave spring.
-
Install the special tool on the side of the center support with the long support legs.
Use Special Service Tool: 307-300
Gauge Bar, Shim Selection.
-
Using a depth gauge, measure and record as measurement
A, the distance from the top of the special tool to the contact surface
of the low/reverse clutch piston.
Use Special Service Tool: 307-300
Gauge Bar, Shim Selection.
-
Measurement B
Using a depth gauge, measure and record as measurement
B, the distance from the top of the special tool to the leg surface of
the center support.
Use Special Service Tool: 307-300
Gauge Bar, Shim Selection.
-
Subtract measurement B from measurement A and record as measurement C.
Description
|
Reading
|
Measurement A
|
|
Measurement B
|
|
Subtract measurement B from measurement A and record as measurement C
|
|
-
Install the special tool on the transmission case.
Use Special Service Tool: 307-300
Gauge Bar, Shim Selection.
-
Using a depth micrometer, measure and record as
measurement D, the distance from the special tool to the top of the
One-Way Clutch (OWC).
Use Special Service Tool: 307-300
Gauge Bar, Shim Selection.
-
Using a depth gauge, measure and record as measurement
E, the distance from the top of special tool to the top of the
low/reverse clutch at 3 different points and average the 3 distances.
Use Special Service Tool: 307-300
Gauge Bar, Shim Selection.
-
Subtract measurement E from measurement D and record as measurement F.
Description
|
Reading
|
Measurement D
|
|
Measurement E
|
|
Subtract measurement E from measurement D and record as measurement F
|
|
-
Subtract measurement F from measurement C to get the
low/reverse clutch clearance. The clearance should be between 0.829 mm
(0.032 in) and 2.023 mm (0.079 in). If the clearance is out of range,
check the low/reverse clutch pack for correct installation. If the
low/reverse clutch pack is correctly installed, install a new clutch
pack.
Description
|
Reading
|
Measurement C
|
|
Measurement F
|
|
Subtract measurement F from
measurement C and check to see if it is within range of 0.829 mm (0.032
in) and 2.023 mm (0.079 in)
|
|
-
NOTE:
When the low/reverse clutch is correctly installed, the wave spring is on top.
Remove the top low/reverse clutch steel plate and wave
spring and correctly install the plates back in the transmission case.
-
Wave spring
-
Steel plate
-
NOTE:
Hold the center support square to the front of the
transmission during installation to prevent cocking/binding.
NOTE:
Be sure the center support is installed with the
long support legs facing down and the feed holes facing the front of the
transmission.
Install the center support with the long legs facing
down and the feed holes aligned with the feed holes in the transmission
case.
-
Long center support legs face down
-
Feed holes face the front of the transmission case
-
Clutch air bleeds
-
-
Install the No. 5 thrust bearing
-
Install the No. 6 thrust bearing
-
Install the center planetary sun gear.
-
Install the center carrier/front ring gear assembly.
-
-
Install the No. 7 thrust bearing
-
Install the No. 8 thrust bearing
-
Install the front planetary/rear ring gear assembly.
-
Install the forward (1, 2, 3, 4) clutch wave spring.
-
Soak the forward (1, 2, 3, 4) clutch pack in transmission fluid.
Material: Motorcraft® MERCON® LV Automatic Transmission Fluid
/ XT-10-QLVC
(WSS-M2C938-A)
(MERCON® LV, )
-
Install the forward (1, 2, 3, 4) clutch pack.
-
Install the forward (1, 2, 3, 4) clutch pressure plate.
-
NOTICE:
Be sure to install the forward (1, 2, 3, 4) clutch
beveled snap ring with the flat side facing down or the snap ring can
come loose, causing damage to the transmission.
Install the forward (1, 2, 3, 4) clutch beveled snap
ring with the flat side down with the gap facing the front of the
transmission.
-
Seat the snap ring in the snap ring groove.
Use the General Equipment: Flat Headed Screw Driver
-
NOTE:
The forward clutch pressure plate travel is limited
by the snap ring and the top of the center support legs. Placing the
dial indicator on the pressure plate will not accurately measure total
clutch pack clearance.
Install the special tool or a dial indicator on the
transmission case and position the plunger on the lower (1, 2, 3, 4)
clutch friction plate.
Use Special Service Tool: 100-002
(TOOL-4201-C)
Holding Fixture with Dial Indicator Gauge.
-
Install the new low/reverse and forward (1, 2, 3, 4) clutch main control-to-transmission case seals.
-
Apply 172 kPa (25 psi) of air pressure to the forward
(1, 2, 3, 4) clutch piston port while recording the clutch pack
clearance on the dial indicator. The clearance should be between 1.158
mm (0.0455 in) and 2.492 mm (0.098 in). If the clearance is out of
range, check the forward (1, 2, 3, 4) clutch pack for correct
installation and the transmission for correct assembly. If the forward
(1, 2, 3, 4) clutch pack is correctly installed, install a new forward
(1, 2, 3, 4) clutch pack.
Refer to: Specifications (307-01B Automatic Transmission - 6-Speed Automatic Transmission – 6F35, Specifications).
Use Special Service Tool: 100-002
(TOOL-4201-C)
Holding Fixture with Dial Indicator Gauge.
-
Install the front planetary sun gear and shell assembly.
-
Install the park pawl.
-
Install the park pawl pin and spring.
-
Install the park pawl actuator rod in the TR sensor. Position the park
pawl aside and position the park pawl actuator rod and the TR sensor in
the transmission case.
-
Install the manual control shaft and align the manual control shaft pin holes.
-
Install the manual control shaft pin.
Use the General Equipment: Punch
-
NOTICE:
Make sure to hold the manual control lever while
tightening the manual control lever nut or damage to the manual control
lever and park components will occur.
Install the manual control lever and the manual control lever nut.
Torque:
18 lb.ft ( 24 Nm)
-
Install the 5 new clutch feed seals.
-
Position the transmission fluid baffle in place and install the transmission fluid baffle bolts.
Torque:
106 lb.in (12 Nm)
-
-
Install the No. 12 thrust bearing
-
Install the No. 10 thrust bearing
-
-
Simultaneously install the drive/driven sprocket and chain assembly.
-
Lightly tap on the driven sprocket to be sure it is fully seated in the case.
-
-
Install the No. 13 thrust washer
-
Install the No. 11 thrust bearing
-
Install the differential transmission fluid baffle.
-
Install the differential sun gear.
-
Install the differential assembly.
-
Install the No. 15 thrust bearing
-
Install the special tool on the input shaft.
Use Special Service Tool: 307-635
Protector, Turbine Shaft Seal.
-
NOTE:
FWD Vehicles.
Assemble the special tools and install a new RH halfshaft seal on the special tool.
Use Special Service Tool: 205-153
(T80T-4000-W)
Handle.
, 307-718
Installer, Axle Seal.
-
NOTE:
FWD Vehicles.
Using the special tools, install the new RH halfshaft seal.
Use Special Service Tool: 205-153
(T80T-4000-W)
Handle.
, 307-718
Installer, Axle Seal.
-
NOTE:
AWD Vehicles.
Assemble the special tools and install a new RH halfshaft seal on the special tool.
Use Special Service Tool: 205-153
(T80T-4000-W)
Handle.
, 307-718-01
Adaper, 307-718.
, 307-718
Installer, Axle Seal.
-
NOTE:
AWD Vehicles.
Using the special tools, install the new RH halfshaft seal.
Use Special Service Tool: 205-153
(T80T-4000-W)
Handle.
, 307-718-01
Adaper, 307-718.
, 307-718
Installer, Axle Seal.
-
NOTE:
Make sure the pump to torque converter housing o-ring remains in position during pump installation.
Install the pump and filter assembly in the torque
converter housing and install the pump-to-torque converter housing
bolts.
Torque:
26 lb.ft (35 Nm)
-
NOTE:
Be sure the sealing surfaces of the torque converter
housing and the transmission housing are free of oil before applying
silicone.
Apply silicone to the sealing surface of the transmission case.
Material: Motorcraft® Ultra Silicone Sealant
/ TA-29
(WSS-M4G323-A8)
-
Install the torque converter housing on the transmission case.
-
NOTE:
Be sure the torque converter housing stud bolt is in the correct location as noted during disassembly.
Install the torque converter housing bolts and the torque converter housing stud bolt.
Torque:
18 lb.ft (24 Nm)
-
Remove the special tool.
Remove Special Service Tool: 307-635
Protector, Turbine Shaft Seal.
-
Install the TSS sensor and the TSS sensor bolt.
Torque:
89 lb.in (10 Nm)
-
Install the OSS sensor and the OSS sensor bolt.
Torque:
89 lb.in (10 Nm)
-
Install the new main control-to-transmission case separator plate and align it on the stud and the guide pin.
-
NOTE:
Be sure that the manual pin (part of the TR sensor) is correctly installed in the manual valve.
Position the main control assembly in place and align the manual valve on the TR sensor.
-
Install the main control nut hand-tight.
-
Install the short main control-to-transmission case bolts hand-tight.
-
Install the long main control-to-transmission case bolts hand-tight.
-
Tighten the main control-to-transmission case bolts and the main control nut in a crisscross pattern.
Torque:
89 lb.in (10 Nm)
-
Position the TR sensor detent spring in place with the alignment tab in
the alignment hole and install the TR sensor detent spring bolt.
Torque:
115 lb.in (13 Nm)
-
NOTE:
Be sure the main control-to-cover seal is installed with the holes facing up.
Install the main control-to-cover seal.
-
Connect the TR sensor electrical connector.
-
Connect the OSS sensor electrical connector.
-
Clean and inspect the main control cover gasket, replace if necessary.
-
NOTE:
Install the main control cover stud bolts in the correct location as noted during disassembly.
Install the main control cover and the main control cover bolts and stud bolts.
Torque:
106 lb.in (12 Nm)
Auto-Start-Stop
-
Clean and inspect the transmission fluid auxiliary pump supply tube and check ball.
-
Check ball (part of the transmission fluid auxiliary pump supply tube)
-
Install the transmission fluid auxiliary pump supply tube assembly.
-
Install the transmission fluid auxiliary pump gasket.
-
Install the transmission fluid auxiliary pump and new bolts.
Torque:
115 lb.in (13 Nm)
All vehicles
-
NOTICE:
The torque converter is heavy. Be careful not to drop it or damage will result.
Using the special tools, install the torque converter.
Use Special Service Tool: 307-091
Handle, Torque Converter.
-
Install the special tool.
Install Special Service Tool: 307-566
Retainer, Torque Converter.
-
Remove the transmission from the bench-mounted holding fixture.
Remove Special Service Tool: 307-003
(T57L-500-B)
Holding Fixture, Transmission.
-
Remove the special tool.
Remove Special Service Tool: 307-725
Mounting Fixture, Bench.
Special Tool(s) /
General Equipment
307-636Alignment Pins- Valve BodyTKIT-2008ET-FLMTKIT-2008ET-ROW
Flat Headed Screw Driver
Magnetic Socket
Long Nose Pliers
Main Control Valve Body and Solenoid Body
Remove the solenoid body-to-valve body bolts and separate the solenoid body from the valve body...
Special Tool(s) /
General Equipment
205-153
(T80T-4000-W)
Handle
206-084Installer, Wheel Speed Sensor RingTKIT-2003-FLM/LMTKIT-2003D-F
307-664Case Bushing InstallerTKIT-2009OP-FLMTKIT-2009OP-ROW
Flat Headed Screw Driver
Hydraulic Press
Materials
Name
Specification
Loctite® 6481835922
WSK-M2G349-A4
DI..
Other information:
Special Tool(s) /
General Equipment
Knife
Removal
NOTE:
Removal steps in this procedure may contain installation details.
Remove the front bumper cover.
Refer to: Front Bumper Cover (501-19 Bumpers, Removal and Installation).
NOTE:
LH side only.
Detach the retainer and position the wiring harness aside.
..
U0100:87
Normal Operation and Fault Conditions
The BECMB uses information contained in messages from the PCM sent on the HS-CAN1 .
DTC Fault Trigger Conditions
DTC
Description
Fault Trigger Conditions
U0100:87
Lost Communication with ECM/PCM “A”: Missing Message
..